ABL provides a range of finishing services including powder coating and anodising.
Anodising
ABL has over 35 years of anodising experience.
We are one of a very few companies in the UK that combine fabrication and anodising on the same site which has the key benefit of minimising handling resulting in higher quality output and reduced costs.
We anodise aluminium extrusion, aluminium sheet and castings every day, supplying a vast range of domestic, consumer, retail and industrial sectors.
Anodised Finishes include:
- Natural (silver) AA3 to AA25
- Special Bespoke Colours
- Black
Overview of anodising
Anodising is an electrolytic process that increases the thickness of the natural oxide layer on the surface of metals. The process is called anodising because the part to be treated forms the anode electrode of an electrolytic cell. Anodising is most commonly used on aluminium, but it can also be used on other metals such as magnesium and titanium.
The oxide layer formed during anodising is very hard and durable. It is also resistant to corrosion and wear. This makes anodised metals ideal for use in a variety of applications, including:
- Automotive: Anodised aluminium is used in a variety of automotive applications, such as car trim, wheels, and engine components.
- Aerospace: Anodised aluminium is used in a variety of aerospace applications, such as aircraft wings, fuselage panels, and landing gear.
- Construction: Anodised aluminium is used in a variety of construction applications, such as window frames, doors, and siding.
- Electronics: Anodised aluminium is used in a variety of electronic applications, such as circuit boards, heat sinks, and enclosures.
In addition to its functional properties, anodising can also be used to improve the appearance of metals. Anodised aluminium can be dyed in a variety of colours, and it can also be given a variety of textures. This makes anodised aluminium a popular choice for decorative applications.
The benefits of anodising
- Increased corrosion resistance: Anodising increases the thickness of the natural oxide layer on the surface of metals, which makes them more resistant to corrosion.
- Increased wear resistance: Anodising increases the hardness of metals, which makes them more resistant to wear.
- Improved appearance: Anodised metals can be dyed in a variety of colours and given a variety of textures, which makes them a popular choice for decorative applications.
- Environmentally friendly: Anodising is an environmentally friendly process that does not produce harmful emissions.
Anodising FAQs
What is Anodising?
Anodising is an electrochemical process that increases the thickness of the natural oxide layer on the surface of metals. The process is called Anodising because the part to be treated forms the anode electrode of an electrolytic cell. Anodising is most commonly used on aluminium, but it can also be used on other metals such as magnesium and titanium.
How does Anodising work?
The Anodising process is carried out in an electrolytic bath, which is a solution of an electrolyte. The electrolyte is typically an acid, such as sulfuric acid or phosphoric acid. The metal to be Anodised is immersed in the electrolyte and an electric current is passed through the solution. The current causes the metal to oxidise, forming a layer of oxide on the surface. The thickness of the oxide layer can be controlled by varying the voltage and current of the electric current.
What are the benefits of Anodising?
Increased corrosion resistance: The oxide layer formed during Anodising is very hard and durable, making the metal more resistant to corrosion.
Increased wear resistance: Anodising also increases the hardness of the metal, making it more resistant to wear.
Improved appearance: Anodised metals can be dyed in a variety of colors and given a variety of textures, making them a popular choice for decorative applications.
Environmentally friendly: Anodising is an environmentally friendly process that does not produce harmful emissions.
What are the different types of Anodising?
There are several different types of Anodising, each with its own unique properties. Some of the most common types of Anodising include:
Sulfuric acid Anodising: This is the most common type of Anodising and is used for a wide variety of applications.
Chromic acid Anodising: This type of Anodising produces a harder and more wear-resistant oxide layer than sulfuric acid Anodising.
Hard Anodising: This type of Anodising produces the thickest oxide layer, making it the most resistant to corrosion and wear.
Decorative Anodising: This type of Anodising is used to create a variety of colours and textures on Anodised metals.
Powder Coating
ABL’s commitment to a one stop shop includes the provision of a powder coat facility.
Components of up to 6 metres can be powder coated with all RAL colours, including translucents, being available. We powder coat aluminium extrusion, sheet, components, castings, flashings and pressings for a wide range of market sectors – many demanding the highest possible surface finish.
Powder Coated Finishes include:
- no risk of running or blistering
- consistent surface appearance (colour and texture)
- powder coatings are able to withstand knocks and abrasions
- powder coated components can be used in internal and external environments – they offer good UV and corrosion resistance
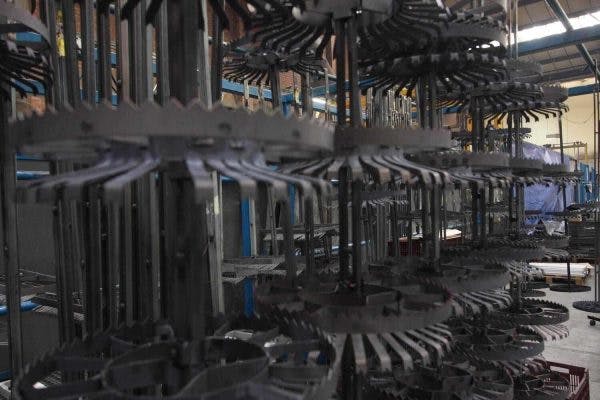
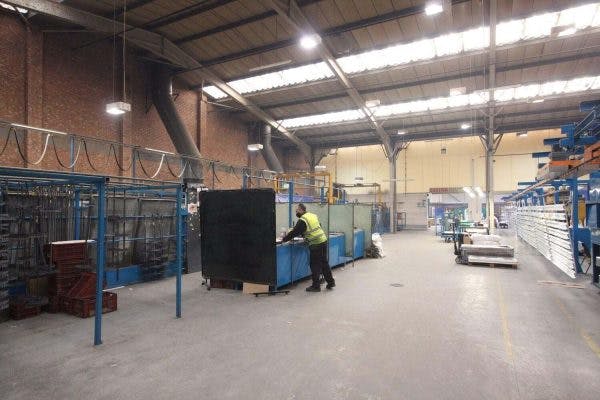
Understanding Anodising and its benefits
Not sure how anodising can benefit your product or want to understand more about anodising?
ABL can offer the appropriate supporting QA documentation for anodising and polishing processes which allows us to supply the automotive industry, where process capability is key.